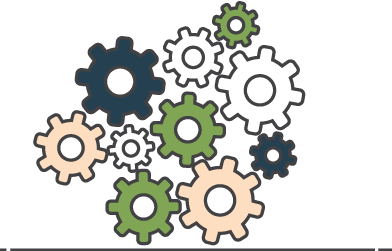
The Project
A rapidly-growing wholesale pickle manufacturer found itself needing to automate its production data processing to accommodate its increasing volume. As a food manufacturer, it is required to track the origins of every ingredient and packaging component through to customer shipments and meet stringent reporting requirements.
When they contacted Fox Wyndrum Associates, the company was collecting and maintaining this data manually. At multiple points during ordering, receiving, production, packaging, labeling and shipping, lengthy product and lot coding was handwritten by workers, then transferred to various ledgers and then again to spreadsheets. The process was extremely inefficient and highly susceptible to error.
The Challenges
The very data-heavy process was further complicated by a fast-paced manufacturing process and frequent in-line ingredient changes. With uptime a key concern, the solution had to collect data seamlessly in a real-time process that allowed the data to flow from one step to the next, controlling the process. It needed to ensure that all data elements were ensured to be collected for every sale unit created and that each product lot batch could be instantly linked to it’s underlying ingredient and packaging sources. The company also sold product under three labels out of two locations which needed to be clearly delineated.
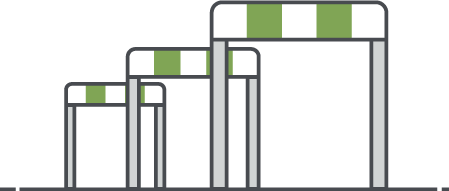
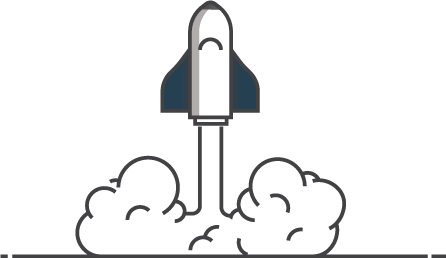
The Solution
Fox Wyndrum Associates developed an end-to-end web-based manufacturing system for the company, utilizing tablets on the production floor to eliminate paper processing. It maintains raw materials and finished goods inventory, tracks purchase orders, customer orders and shipments, and gives management robust reporting for sales, production, inventory projections and more. Sales data is readily exported to an external accounting package. The underlying data model creates extensive data controls that allows “smart” options to efficiently filter user selections.
The implemented system is composed of several interwoven modules:
Sales Order Maintenance
The sales order process features streamlined entry with user- and location-level customer and product access to ensure correct data collection. Customer-specific product numbers are supported. The Data feeds into shipping calendars and delivery schedules. It is combined with inventory information for production planning.
Purchase Orders and Inventory Receiving
Purchasing and receiving tens of thousands of pounds of produce a week with a three-to-four day turnover necessitated an efficient but flexible purchase order entry and receiving process. As the first “building block” of the ingredient-trace chain, it accurately captures product origins and lots. The process generates labels clearly identifying each item received, allowing raw materials to be scanned into inventory then out to production.
Manufacturing Production Process
The production module is the most dynamic part of the company’s manufacturing system. It combines separate functionality of three production components:
The produce ingredients are pulled from inventory and are put into production lines on the tablet.
The brine mixing operators , working separately, record newly created batches using pre-defined recipes to trace ingredient lot usage. They are able to control release into an unlimited number of production lines or to storage.
Product batch supervisors , pulling data from produce and brine active on the lines, are able to quickly pair brine and produce batches in real time on the production floor, generating unique end-product batch lot numbers and barcodes linked to all included source ingredients and packaging.
Finished Goods Inventory and Shipping
The system generates transactions in and out of finished goods inventory, maintaining individual product batch lot identification through to end customer delivery. The robust reporting functions support shipment scheduling, pick and pack, and inventory control management. The system also generates all necessary shipping documentation to meet regulatory guidelines.
Have a unique business need? Tell us about it!
Do you have a process that doesn’t “fit” an off-the-shelf solution? Do you have disparate systems that need time- and money-saving integration? Contact us today by calling 908-791-0100 or using the form below to schedule a FREE, NO-OBLIGATION conversation to discuss your needs .